Bijscholing van leiderschap om te voldoen aan de eisen van automatisering
.jpeg)
• Automation is driving the need for upskilling in industries to match the pace of transformation and retain talent.
• Specific job roles and skills are in high demand due to automation, such as engineers and sustainability specialists.
• Soft skills like analytical thinking and leadership are crucial for businesses to develop alongside technical skills to survive automation.
• Manufacturers need to prioritize leadership development and training delivery to support their workforce through automation.
• Talent development in manufacturing leads to increased employee satisfaction, higher retention rates, and ultimately, improved business profits.
As automation dictates industries’ futures, upskilling initiatives need to match the speed of its transformation to retain talent and equip them with future skills.
L&D experts Robert-Jan Stolk, Kevin Coolen and Berend Kirch sat down together to discuss automation, skill gaps and leadership upskilling – taking the manufacturing industry as an example.
Automation is changing future skills. Over 75% of companies industry-wide will integrate more automation into operations by 2028 to improve efficiency and profit. While its arrival will bring more capabilities to businesses, what does automation mean for their future supply of skilled labor and talent retention?
Automation has the potential to be a significant driver of employment. Out of the companies integrating automation, 50% forecast job growth versus 25% expect job losses. This growth, however, depends not only on the types of skills and jobs automation demands, but also on the upskilling opportunities businesses offer their talent.
Download your manufacturing upskilling guide
Automation fuels specific job roles & skills
Automation is increasing demand for specific jobs and skills. With deeper integration of automation in business operations, engineers and sustainability specialists are expected to rank top of recruitment agendas. The World Economic Forum predicts that technology and automation will drive these roles the fastest:
- AI and Machine Learning Specialists
- Sustainability Analysts
- Renewable Energy Engineers
- Solar Energy Installation
- System Engineers
There’s a clear focus on systematic engineering and creating more sustainable practices with AI. And with these fast-growing jobs, 44% of skills could be disrupted by 2028. Here are key future soft skills businesses need to develop to survive automation:
- Analytical thinking
- Creative thinking
- Self-efficacy skills such as resilience, flexibility and agility
- Leadership skills
As the demand increases for technical talent such as engineers, businesses will also have to develop their soft skills to manage automated processes and have leaders in place to support teams through change.
However, people’s skill development isn’t moving at the same speed as AI transformation. 60% of talent will require training within the next 5 years, yet only 50% of talent have access to adequate training.
To contextualize the skill solutions required for workforce upskilling, automation in smart manufacturing is a prime example.
Future skills for manufacturing operations
The forecasted future skills and occupations are especially relevant to the manufacturing industry. With 83% of Belgium and 90% of German manufacturers prioritizing smart factories to optimize productivity with industry 4.0, manufacturing engineer skills will be in high demand.
However, manufacturers will require talent with mixed skill sets who can think analytically and solve problems to work with new technical and sustainable systems, such as:
- Machine vision for automated inspection to improve product quality
- AI-based applications to predict energy consumption and emissions for the future
But manufacturers also need the leadership skills and talent pipeline in place to manage industry 4.0 and support talent in new operation roles.
An expert deepdive into manufacturing workforce upskilling
With automation transforming the industry and skill demands changing, we asked industry experts Robert-Jan Stolk, Kevin Coolen and Berend Kirch to pinpoint workforce challenges in manufacturing and how HR leaders can support and develop their operation teams to prepare for future changes.
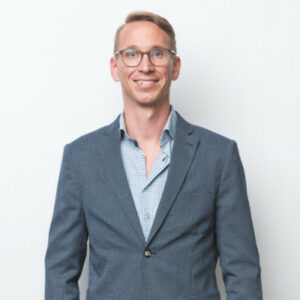
Robert-Jan Stolk, Sales & Training Consultant
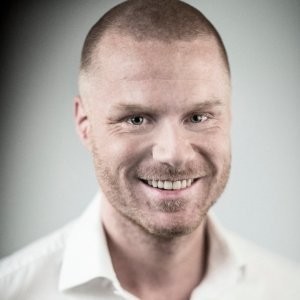
Kevin Coolen, L&D Consultant
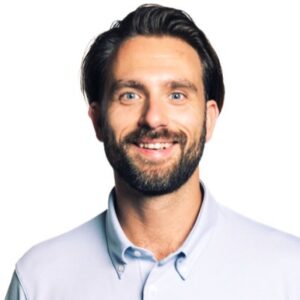
Berend Kirch, Trainer & Leadership Program Manager
Which key skills should manufacturers prioritise?
Berend Kirch: “As a starting point, leaders are key to manufacturing success. Typically on the operational side, I see high turnover and low engagement rates in teams because of fixed leadership styles.
Leaders are task-oriented and don’t communicate well with their teams in high production environments. Which makes sense because they’re under extreme time and cost pressure to produce results and operate machinery.
So these team leaders are focused on results and it’s reflected in their leadership styles. They quite often use a directive approach and this one-way communication style isn’t motivating for their team.
That’s why when I first look at manufacturers’ training strategies, I often start with leadership development for first-time as well as experienced leaders on the operation side.”
Kevin Coolen: “I can add two points here. The first is cultural. Manufacturing production teams are mostly male-dominanted and tend to be characterized by a fixed-mindset so something like a feedback culture doesn’t really exist. When I’m talking to clients, talent retention seems to be a huge issue because they struggle to create the right working environments.
And second, 60% to 70% of manufacturing talent is in operations, but the budget is concentrated on developing management on the other side of the business. From a strategic standpoint, this isn’t where learning interventions are most critical since the majority of work is in operations. There are plenty of options for management upskilling but hardly any for operators despite their appetite for learning.
For example, if I look at leaders operating on harbor docks, there’s more to their work than technical skills. They are dealing with people from different social and cultural backgrounds, meaning they need flexible communication and leadership skills to manage different situations. Not all people in management positions are equipped to have these conversations.”
How can manufacturers best deliver the training?
Robert-Jan Stolk: “Coming back to Kevin’s earlier point on learning interventions, delivering training in the manufacturing industry can be very challenging. Talent’s working hours are unpredictable so once I’ve designed a learning intervention for a client, finding a set time to deliver the training can be difficult.
Plus if we’re focusing on the operation side, you have to be mindful of disrupting production. How can you deliver the training and limit the impact on production costs? When you look at this from C-level’s management perspective, you can understand their reluctance.“
Kevin Coolen : “Yes and it’s clear that digital solutions are key to upskilling manufacturers’ workforce. It’s even harder to deliver training to older talent because some of them don’t even have an email to access learning materials.
I’m advising manufacturing clients more and more to adopt training solutions such as Virtual Reality because it’s time and cost efficient and we can bring the training straight to talent without administration issues. Plus it is an effective way to engage and bond operational teams.”
What is the impact of talent development in manufacturing?
Robert-Jan Stolk: “From experience, the main benefit is increased employee satisfaction which leads to higher retention rates. And if we take this a step further, this doesn’t only save on recruitment costs, but leads to higher quality of work and more revenue. It’s hard to measure the exact number but talent training is connected to business profits.”
Kevin Coolen: “If we look at the other types of impact, upskilling is key to succession management and leadership retention. Management rewards talent who are skilled in their speciality with promotion into a leadership role. But you also have to support them to develop the right skills, otherwise ‘you lose a good employee and get a bad manager’.
In practice we see that people join companies but leave managers. I realize it is a giant cliché but that does not make it less true. If you can give managers – especially first-time leaders – the skills to create the right working environment for their team, they will stay longer at your company and ultimately reduce your spending on talent attraction.”
Robert-Jan Stolk: “And to add to Kevin’s point on leadership retention, I often see managers that performed well in their specialty and therefore received a promotion, but they’re stuck between two jobs. They’re balancing their workload around 50/50 between their old role and their new leadership role. When manufacturers’ don’t invest in supporting them, this transition is quite draining and stressful.”
Berend Kirch: “For me, the biggest impact is the ability to change operation leaders and let them experience different leadership styles. I don’t just see positive responses in their teams, but also less stress on themselves as leaders. As their communication improves and they shift from being task-oriented, they’re able to spread the workload and responsibility by creating a culture of trust.”
What is the role of leadership when automated processes increase?
Berend Kirch: “Even though operations are becoming more automated, you can never automate people management. Just because manufacturers need talent with more technical skill sets to manage machinery, that doesn’t mean this talent can do without people support. They need to be motivated and engaged so I only see the role of leaders in manufacturing growing. With automation moving increasingly towards task- and efficiency focus, the need for human centered leadership is greater.”
Interested to know more about manufacturing and talent upskilling strategies? Download Lepaya’s manufacturing upskilling guide for a 5-step guide to upskill your people.
Download your manufacturing upskilling guide
This article was originally published on chro.nl
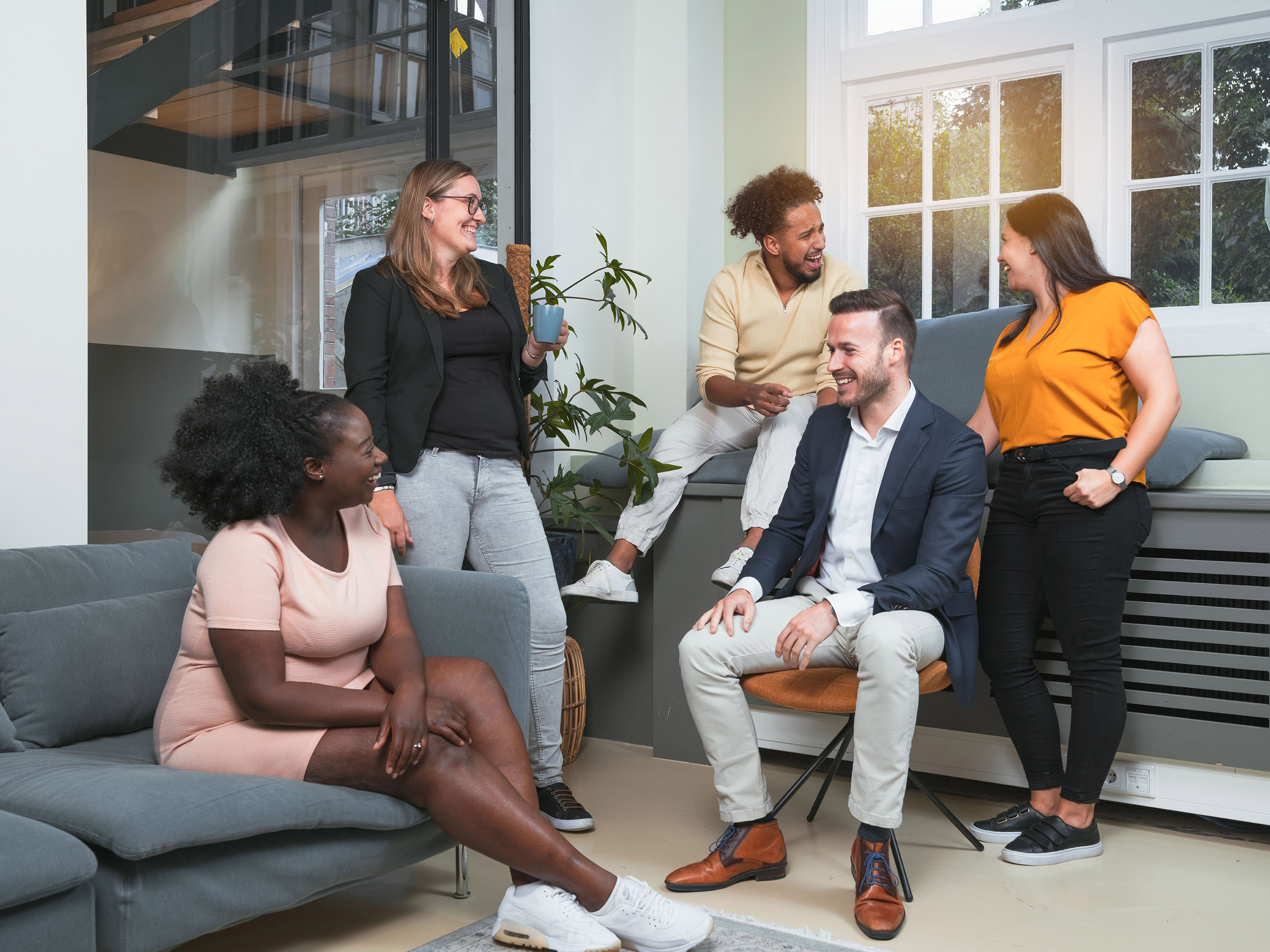
We bieden een schaalbare oplossing voor de opleiding van werknemers. Hiermee kun je je mensen continu bijscholen.
Boek een gesprek.png)